Comprehensive Guide to Metal Stamping: Strategies, Applications, and Benefits
Comprehensive Guide to Metal Stamping: Strategies, Applications, and Benefits
Blog Article
The Evolution of Steel Stamping Procedures: Advancements and Applications
The realm of metal marking procedures has experienced a transformative trip marked by continuous technology and adaptation to satisfy the needs of modern commercial techniques. The applications span across a spectrum of sectors, each profiting uniquely from the improvements in steel marking processes.
Conventional Steel Marking Strategies
Traditional metal stamping methods have actually long been the structure of manufacturing processes in various markets because of their performance and accuracy. The procedure involves forming a metal sheet or coil into a preferred shape by pressing it between a die and a punch. This technique is commonly made use of for creating large amounts of get rid of high accuracy at a fast pace.
Among the key advantages of conventional metal stamping methods is the capability to keep limited resistances, making sure that each component satisfies the needed requirements continually. This degree of accuracy is necessary in sectors such as vehicle, aerospace, and electronic devices, where even minor discrepancies can result in significant issues.
In addition, typical steel marking methods offer cost-effective services for mass production compared to various other producing techniques. The ability to mark components in quick succession decreases manufacturing time and decreases labor costs, making it an eye-catching choice for organizations aiming to enhance their manufacturing procedures.
Introduction of High-Speed Stamping

One of the vital advantages of high-speed marking is its ability to maintain precision and uniformity even at increased processing rates. This precision is vital in industries where limited tolerances and complex designs are needed. In addition, high-speed stamping enables the processing of a variety of materials, consisting of aluminum, stainless-steel, and copper, further broadening its applicability throughout various markets.
Furthermore, the introduction of high-speed marking has allowed suppliers to satisfy the expanding demand for complex parts in industries such as vehicle, aerospace, here are the findings and electronic devices (Metal Stamping). By leveraging the speed and precision of high-speed stamping innovation, firms can enhance their competitiveness in a quickly advancing market landscape
Developments in Tooling Innovation
With the evolution of high-speed marking allowing improved precision and performance in steel developing processes, the area of metal stamping has actually seen considerable developments in tooling technology. Tooling technology plays a critical function in metal marking procedures, influencing variables such as item quality, manufacturing rate, and overall see post cost-effectiveness.
By utilizing these sophisticated products, tooling manufacturers can create passes away and mold and mildews that withstand the high pressures and temperatures involved in steel stamping processes, resulting in longer device life and improved manufacturing efficiency. In general, these improvements in tooling modern technology have transformed the steel marking sector, permitting manufacturers to achieve higher levels of precision, efficiency, and expense financial savings.
Assimilation of Automation in Marking
As automation proceeds to improve the landscape of steel marking procedures, the combination of automated systems has actually become increasingly prevalent in modern production centers. Automated systems supply countless advantages in steel marking, consisting of boosted effectiveness, enhanced accuracy, and enhanced safety. By incorporating automation right into marking procedures, producers can decrease cycle times, reduce material waste, and maximize manufacturing throughput.
One of the vital elements of automation in stamping is making use of robot arms for tasks such as product handling, part adjustment, and high quality evaluation (Metal Stamping). These robotic systems can execute repeated and labor-intensive jobs with rate and precision, liberating human operators to concentrate on even more complex procedures. Furthermore, automation permits real-time tracking and adjustment of marking processes, causing higher general process control and quality control
In addition, the combination of automation in marking makes it possible for producers to attain consistent component quality, satisfy limited tolerances, and boost overall efficiency. As technology remains to breakthrough, the role of automation in steel marking processes is expected to broaden better, driving advancement and efficiency in the production market.
Applications Across Diverse Industries
Incorporating steel marking processes throughout varied markets showcases the versatility and adaptability of this production method. Additionally, the device market benefits from steel stamping procedures to produce parts for fridges, washing machines, and various other home appliances. The flexibility of metal marking processes have a peek at this website makes it a valuable production technique throughout various sectors, demonstrating its importance in modern-day production procedures.
Conclusion
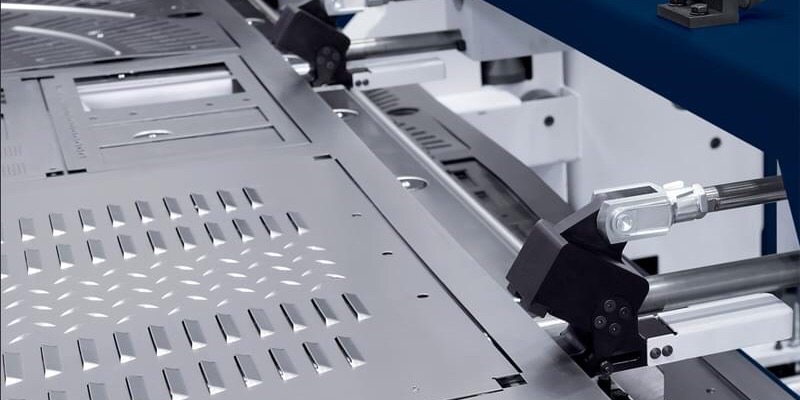
Report this page