An Unbiased View of Alcast Company
An Unbiased View of Alcast Company
Blog Article
Unknown Facts About Alcast Company
Table of ContentsSome Known Details About Alcast Company The 7-Minute Rule for Alcast CompanyFacts About Alcast Company UncoveredThe Greatest Guide To Alcast CompanyAlcast Company Fundamentals ExplainedNot known Facts About Alcast Company
The subtle difference hinges on the chemical content. Chemical Comparison of Cast Aluminum Alloys Silicon promotes castability by minimizing the alloy's melting temperature and improving fluidness throughout casting. It plays a critical duty in permitting detailed mold and mildews to be filled up precisely. Furthermore, silicon contributes to the alloy's strength and wear resistance, making it valuable in applications where resilience is vital, such as auto components and engine parts.It likewise enhances the machinability of the alloy, making it easier to refine into ended up products. In this means, iron contributes to the overall workability of light weight aluminum alloys.
Manganese adds to the stamina of aluminum alloys and improves workability (aluminum metal casting). It is frequently used in functioned light weight aluminum products like sheets, extrusions, and accounts. The presence of manganese aids in the alloy's formability and resistance to fracturing during manufacture processes. Magnesium is a lightweight component that offers toughness and effect resistance to light weight aluminum alloys.
Alcast Company for Dummies
It allows the production of light-weight components with superb mechanical homes. Zinc enhances the castability of aluminum alloys and assists regulate the solidification procedure throughout casting. It enhances the alloy's stamina and solidity. It is typically located in applications where intricate forms and great details are needed, such as attractive castings and specific auto components.
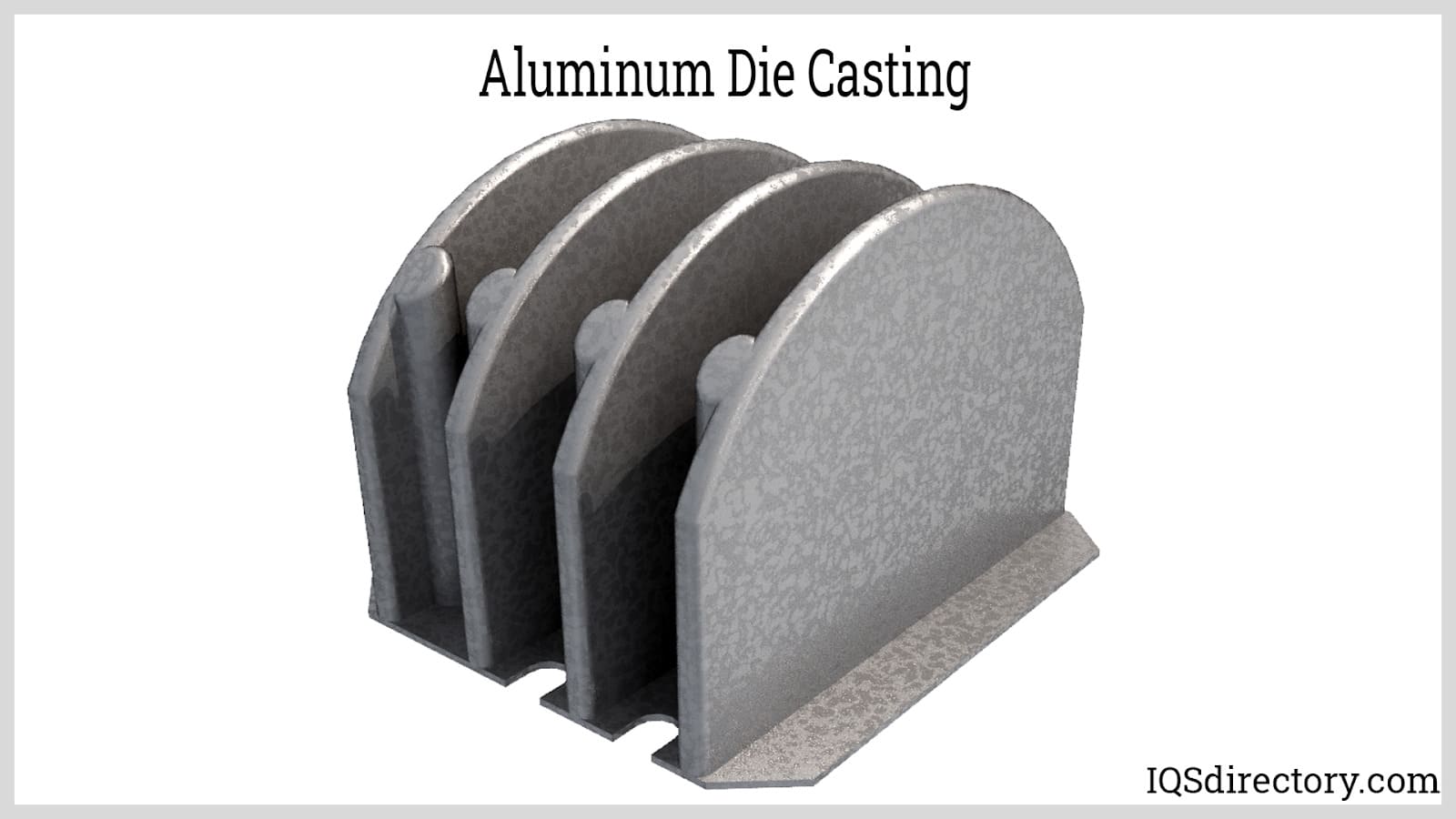
The main thermal conductivity, tensile stamina, yield stamina, and elongation differ. Select suitable basic materials according to the performance of the target product created. Amongst the above alloys, A356 has the highest thermal conductivity, and A380 and ADC12 have the lowest. The tensile limit is the opposite. A360 has the ideal yield toughness and the highest possible prolongation rate.
Getting The Alcast Company To Work

In accuracy casting, 6063 is appropriate for applications where complex geometries and premium surface area coatings are critical. Instances consist of telecommunication enclosures, where the alloy's premium formability enables streamlined and cosmetically pleasing layouts while maintaining structural stability. In a similar way, in the Lights Solutions market, precision-cast 6063 components create classy and effective illumination fixtures that require detailed shapes and good thermal efficiency.
The A360 exhibits remarkable prolongation, making it ideal for facility and thin-walled components. In precision spreading applications, A360 is appropriate for sectors such as Consumer Electronic Devices, Telecommunication, and Power Devices.
Rumored Buzz on Alcast Company
Its special properties make A360 a beneficial selection for accuracy casting in these industries, enhancing item longevity and high quality. Aluminum Castings. Aluminum alloy 380, or A380, is a commonly used spreading alloy with several distinct qualities.
In accuracy casting, light weight aluminum 413 radiates in the Customer Electronics and Power Tools sectors. It's generally made use of to craft elaborate components like mobile phone real estates, camera bodies, and power device casings. Its precision is impressive, with tight resistances approximately 0.01 mm, guaranteeing remarkable product setting up. This alloy's exceptional deterioration resistance makes it an excellent choice for outdoor applications, guaranteeing long-lasting, long lasting products in the discussed markets.
Not known Facts About Alcast Company
The light weight aluminum alloy you choose will significantly impact both the spreading process and the residential or commercial properties of the last product. Due to the fact that of this, you have to make your choice carefully and take an informed strategy.
Establishing the most appropriate aluminum alloy for your application will imply considering a broad range of qualities. The very first group addresses alloy qualities that influence the production process.
Not known Factual Statements About Alcast Company
The alloy you choose for die spreading directly influences several facets of the casting process, like just how very easy the alloy is to collaborate with and if it is susceptible to casting flaws. Warm cracking, likewise understood as solidification fracturing, is a common die spreading problem for aluminum alloys that can lead to inner or surface-level splits or fractures.
Specific light weight aluminum alloys are more prone to hot cracking than others, and your option must consider this. One more usual problem found in the die spreading of light weight aluminum is pass away soldering, which is when the cast sticks to the die walls and makes ejection tough. It can damage both the actors and the die, so you ought to seek alloys with high anti-soldering properties.
Deterioration resistance, which is already a notable characteristic of light weight aluminum, can differ considerably from alloy to alloy and is a crucial particular to consider relying on the environmental problems your item will certainly be subjected to (Casting Foundry). Continue Wear resistance is one more property commonly sought in aluminum items and can separate some alloys
Report this page